
Die Sättel Specialized S-Works Power with Mirror Technology by Carbon und Fizik Antares Adaptive Versus Evo 00 haben nicht nur einen sperrigen Namen, sondern auch das Potential zu einer kleinen Revolution: Durch eine kundenindividuelle Gestaltung könnten diese beiden Sättel den Fahrkomfort deutlich steigern. Wie genau das funktionieren kann, erfahrt ihr in dieser Ausgabe von Dreh-Momente am Dienstag.

Die Kontaktpunkte von Fahrer und Fahrrad entscheiden über Freud oder Leid beim Radfahren. Und weil jede und jeder eine andere Anatomie hat, anders auf dem Rad sitzt und anders damit fährt, ist es häufig trotz großer Auswahl schwierig, eine bequeme Lösung für Sattel, Griffe und Schuhe zu finden. Genau hier könnte Specialized ansetzen und durch individuelle Sättel die Freude am Radfahren vergrößern. Sowohl Specialized als auch Fizik haben sich hierfür mit der Firma Carbon zusammen getan, die das Know-How zu 3D-Druck und Gitterstrukturen beisteuern soll.
Video
Wie funktioniert’s?
Im Grunde steht man mit individuellen Sätteln vor zwei Herausforderungen: Erstens – wie erstellt man das individuelle Modell, und zweitens: wie stellt man es dann her?
Teil 1: Ein individuelles, virtuelles Sattel-Modell
Normalerweise wird ein Sattel entweder von Hand geshaped und anschließend nachmodelliert, um ein Werkzeug herzustellen, oder er wird direkt am Computer konstruiert und dann damit das Werkzeug produziert. Zum konventionellen Vorgehen hatte ich ja schon vor einiger Zeit etwas geschrieben. Das könnte man natürlich auch für jedes Gesäß individuell machen, aber der Konstruktionsaufwand würde die Preise dafür leider recht schlecht bezahlbar machen.

Die von Carbon (übrigens einer der ungeschickteren Namen am Markt, wenn man mich fragt: „Carbon“ ist ein Start-Up aus dem Silicon Valley, das die „CLIP“ genannte „DLS“-Technologie entwickelt hat und entsprechende Materialien und Anlagen vertreibt, aber dazu später mehr. Früher hieß das Unternehmen wenigstens noch Carbon3d, aber jetzt ist es einfach nur verwirrend.) veröffentlichte Case-Study legt ein anderes, automatisiertes Vorgehen nahe: Aus einer Druckverteilung dürfte automatisiert eine passende CAD-Geometrie erzeugt werden. Man darf sich vorstellen, dass man auf einer Messplatte Probe sitzt, wie man es heute schon in einigen Läden üblich ist. Daraus wird dann nicht nur der Sitzknochenabstand ermittelt, sondern alle Informationen genutzt: Wo ist der größte Druck, wie ist er verteilt?


Je nach Druck wird dann die Gitterstruktur engmaschiger oder weiter, mit dickeren oder dünneren Balken gestaltet. Gleichzeitig sollen die Zellstrukturen teilweise so ausgelegt sein, dass sie maximal Energie aufnehmen (eher dämpfen) oder zurückgeben (eher federn). Man sei überrascht gewesen, dass größere Dämpfung nicht unbedingt einen größeren Komfort bedeute, heißt es in der Veröffentlichung. Man darf sich also vorstellen, dass die 14.000 Balken im Inneren des Sattels je nach ermitteltem Druck skaliert und verschoben werden, sodass sich eine individuelle Geometrie ergibt. Spannend wird es dann, wie beispielsweise mit den Lüftungsöffnungen und der Hüllgeometrie umgegangen wird – es ist nicht zu viel gesagt, dass diese automatisierte 3D-Konstruktion eine der größeren Herausforderungen an der ganzen Geschichte darstellt. Dass sich die komplexe, dreidimensionale Gitterstruktur überhaupt herstellen lässt, ist ein Vorzug des 3D-Drucks.

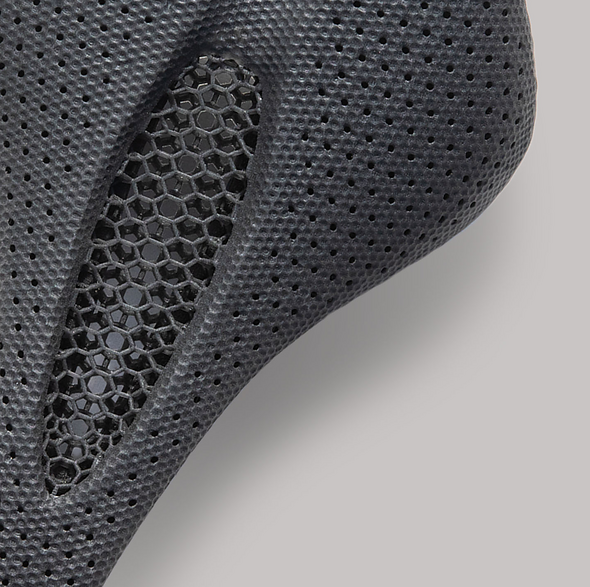
Durch gezielt variierte Rauheit der Oberfläche des Sattels soll sich eine optimale Bewegungsfreiheit und Grip auf dem Sattel einstellen.
Teil 2: Ein individuelles Sattel-Modell herstellen
Bei der Individualteil-Herstellung kommt der nächste Vorzug des 3D-Drucks zum Vorschein. Weil kein Werkzeug verwendet wird, das immer die gleiche Form hat, ist es einer Carbon-Anlage grundsätzlich egal, ob sie immer das gleiche oder nur unterschiedliche Bauteile produziert.

Um eine oder mehrere Satteldecken zu produzieren, wird das Modell virtuell in viele dünne Schichten zerschnitten. Das eint alle additiven Herstellungsverfahren: Es wird Schicht für Schicht aufgebaut, was auch komplexe Geometrie erlaubt. In die Maschine wird zunächst ein lichtaushärtendes Harz in die Wanne eingefüllt und dann die Bauplattform bis fast an die transparente Membran auf der Unterseite der Wanne gefahren. Unterhalb sitzt vereinfacht gesagt ein „Beamer“, der auf der Fläche der Bauplattform jeden Punkt entweder belichten oder nicht belichten kann. Der „Beamer“ zeigt also einfach eine Schnittfläche nach der anderen an, und wo er einen Bauteilschnitt zeigt, härtet dieser zum Bauteil aus. Dann wird die Platte einen Hauch höher gefahren und die nächste Schicht ausgehärtet.
Das Besondere an der Technologie von Carbon: Einerseits wird eine ganze Schicht auf einmal bearbeitet (und nicht wie bei vielen anderen 3D-Druck-Technologien eine Schicht mühsam mit einer Düse oder einem Laser schraffiert), andererseits ist zwischen den Schichten kein Hub aus dem Harzbecken nötig. Hier spielt die Chemie eine wichtige Rolle; denn damit das Bauteil durch den Beamer nicht an der Unterseite der Wanne festgeklebt wird, kann die Reaktion von Harz unter Lichteinwirkung nur in Abwesenheit von Sauerstoff stattfinden. Durch die Membran findet sich aber eine mit Sauerstoff angereicherte Schicht darüber, die so genannte Dead-Zone. Die Reaktion findet dann erst minimal über der Membran statt, wodurch Carbon die Bauplattform fast kontinuierlich aus dem Harz ziehen kann. Diesen Vorgang sollen die beiden Namen „Continous Liquid Interphase Production, kurz CLIP“ und „Digital Light Synthesis, kurz DLS“ beschreiben.
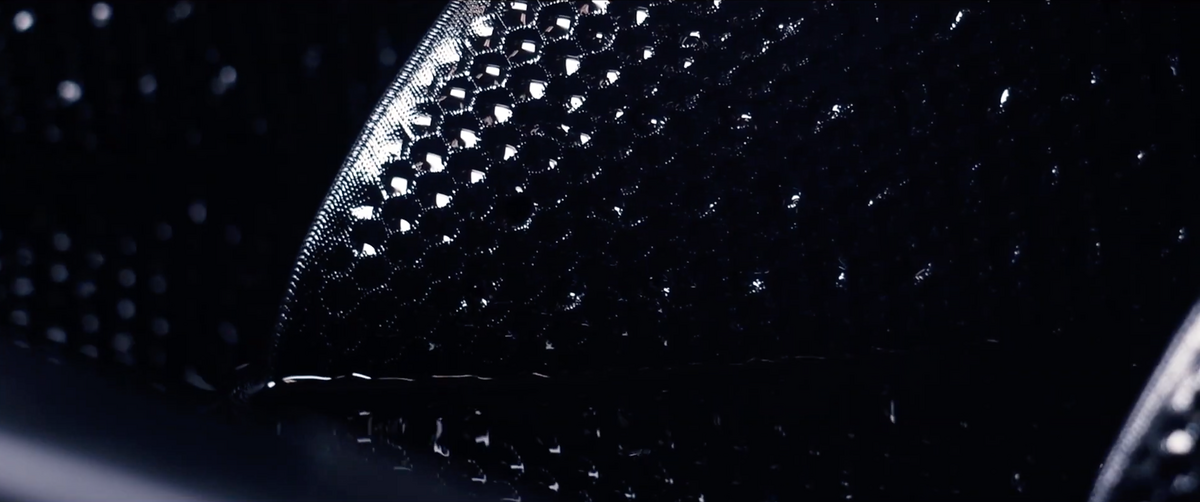
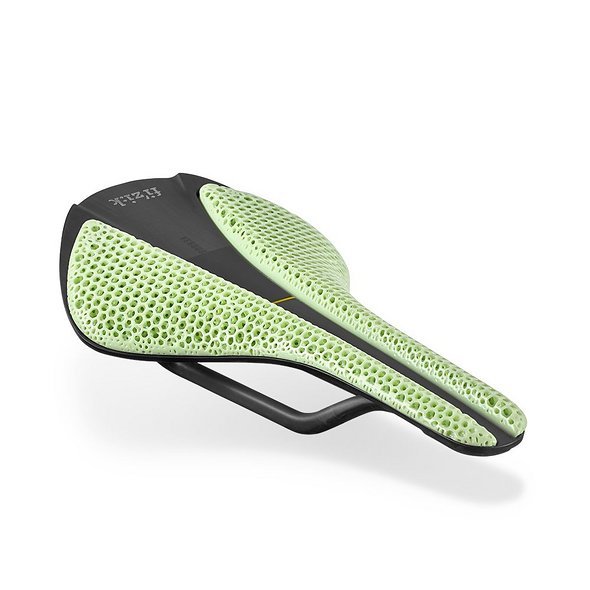

Nach dem eigentlichen „3D-Druck“ müssen die Satteldecken dann noch von der Platte getrennt, gereinigt und nachvernetzt werden – in einem Ofen wachsen die Polymer-Ketten und die finalen Eigenschaften stellen sich ein. Damit wäre die Satteldecke fertig. Fehlt noch das Gestell – dieses wird freilich nicht aus elastischem Polyurethan hergestellt, wir gehen eher von faserverstärktem Kunststoff aus. Bei Fizik gibt es hier zwei verschiedene Schalen in unterschiedlicher Breite; bei Specialized gibt es hierzu noch keinen Kommentar – ob tatsächlich nur eine individuelle Satteldecke auf dem immer gleichen Grundgerüst montiert wird, ist derzeit noch nicht bekannt.
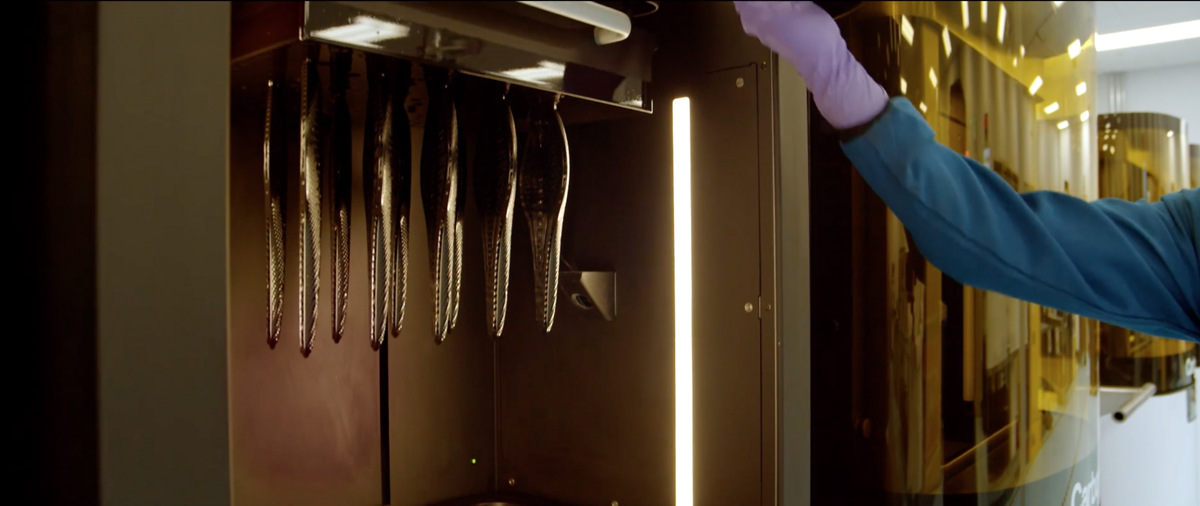
Specialized und Fizik sind übrigens nicht die ersten, die auf die Technologie von Carbon aufmerksam geworden sind: Auch Adidas stellt die Sohlen seiner Futurecraft 4D Sneaker auf den amerikanischen Anlagen her. Individuell ist hier aber – bisher – gar nichts: Die Sneaker werden nicht an den Fuß des Käufers angepasst. Hohe Sammlerwerte erzielen die ständig ausverkauften Teile trotzdem – der Verkaufspreis von 299 € wird aus zweiter Hand zuverlässig überschritten und reicht teilweise in den vierstelligen Bereich. Hinsichtlich der Markteinführung will Fizik schon ein wenig weiter sein als Specialized und hat die Sättel für Ende 2019 angekündigt. Das genaue Vorgehen zur Individualisierung wurde aber noch nicht bekannt gegeben. Bei Specialized soll es in 2020 so weit sein.
Was kommt dabei raus?
Im Gegensatz zu normalem Sattelschaum ist die Gitterstruktur des S-Works Power with Mirror Technology offenporig. Das bedeutet, dass theoretisch viel mehr Luft hindurch strömen kann. Das dürfte aber nicht der große Vorteil sein – spannend ist dagegen, ob die angepasste Härteverteilung tatsächlich einen viel besseren Komfort bedeutet. Davon wird man sich frühestens ab 2020 einen Eindruck verschaffen können. Wir sind bereit, uns vermessen zu lassen und ein neues Level des Sitzkomfort zu erreichen – denn bisher hat auch der bequemste Sattel irgendwann irgendwo irgendwie gedrückt. Was der Spaß dann kostet? Warten wir es ab – teuerer als der 263 € kostende, aktuelle Specialized S-Works Power wird es aber ziemlich sicher …
Alle Artikel der Dreh-Momente-Reihe
- Dreh-Momente am Dienstag: Individuelle Sättel durch 3D-Druck
- Drehmomente am Dienstag: Was spricht für Parallelogramm-Federgabeln?
- Dreh-Momente am Dienstag: Aerodynamik auf dem Mountainbike
- Dreh-Momente am Dienstag: Gefahrenherde im Bike-Alltag
- Dreh-Momente am Dienstag: Wie wird eigentlich ein Sattel entwickelt?
- Dreh-Momente am Dienstag: Rotierende Massen
- Dreh-Momente am Dienstag: Ungefederte Massen
- Dreh-Momente am Dienstag: Lasst uns über Gewicht sprechen
- Dreh-Momente am Dienstag: Wie Danny MacAskills neues Santa Cruz Carbon Trial-Bike entstand
- Dreh-Momente am Dienstag: Ergibt es Sinn, ein Fahrrad aus dem Vollen zu fräsen?
- Dreh-Momente am Dienstag: Dämpfung – was ist das eigentlich?
- Dreh-Momente am Dienstag: Warum werden Bremsscheiben so montiert?
- Dreh-Momente am Dienstag: Gradwanderung – alles eine Frage des Lenkwinkels
- Dreh-Momente am Dienstag: Wo sind eigentlich die echten Steckachsen hin?
Der Beitrag Dreh-Momente am Dienstag: Individuelle Sättel durch 3D-Druck erschien zuerst auf MTB-News.de.